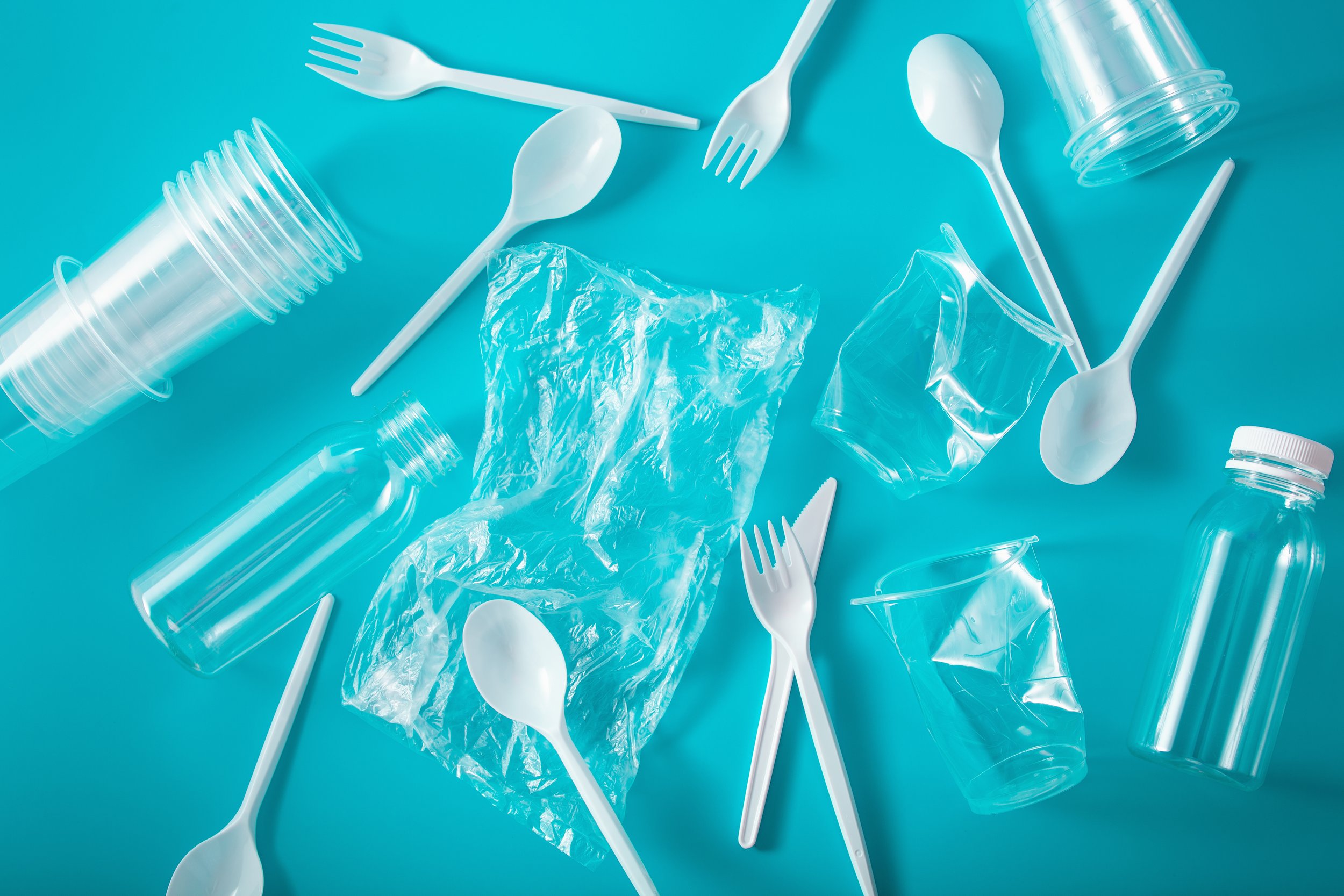
Plastic Innovation
Firstar Fiber, Inc. Integrated Plastic Waste Management System
Firstar Fiber’s Integrated Plastic Waste Management System (IPWMS) will address plastic wastes across the entire range of recyclability and recovery, diverting them from the landfill and the environment in order of the waste hierarchy. With support from the Alliance to End Plastic Waste and the Nebraska Department of Environment and Energy, the infrastructure installation of a plastic pre-processing plant, plastic remanufacturing plant, and additional bolt-on plastic manufacturing facilities, alongside our existing Materials Recycling Facility (MRF) effectively demonstrates solutions for plastic waste across the value chain by highest and best use in a way that is sustainable and replicable wherever there is a need.
Collection Systems
Plastics are collected through several collection systems capturing both residentially and commercially generated materials and agricultural wastes:
Curbside Collection Systems: This project builds on the success of the Hefty® ReNew® Program, capturing hard-to-recycle plastics at the curb alongside regular recycling.
Rural Collection Programs: Plastics are collected through our network of Hub & Spoke recycling partners across the state of Nebraska and beyond
Agricultural Plastic Collection System – Firstar Fiber is developing a collection system targeting agricultural plastics that frequently end up being burned or dumped in the environment due to there being no current recovery options for these plastics. This plastic stream includes single-use ag plastics such as grain bags, grain tarps, bale wrap, feed bags, etc.
Commercial Plastics: First Star Recycling will expand on business and commercial recycling programs to target plastics that may not have current markets for recycling.
2. Traditional Recycling
Plastics that are recyclable by traditional means will continue to be captured and processed by our Mechanical Recovery Facility (MRF). This means that the plastics that currently have good end markets and are valuable for remanufacturing into new products remain as such. The IPWMS is designed to ensure that plastics wastes are processed for their highest and best use.
3. Plastic Pre-Processing Facility (PPRF)
Plastics that are considered notoriously hard-to-recycle, such as films or plastics with limited end markets, will be processed through our plastic pre-processing facility - turning them into plastic feedstock cubes or flake. By processing these low-to-no-value plastics into a cube/flake format, it increases their usability in re-manufacturing processes and they are then able to be used to manufacture products such as plastic lumber, rail ties, fence posts, decking, and wallboard.
A portion of these plastic feedstock cubes will be utilized in our plastic lumber facility as detailed below. The remainder will be available for use in other manufacturing processes. If you are interested in using the feedstock cubes in your process, please contact us here.
4. Plastic Lumber
Our Plastic Lumber facility will be generating approximately 700,000ft of plastic lumber boards in both dimensional lumber and decking boards. Made from 100% hard-to-recycle plastic, this technology generates an attractive high quality board while also targeting plastics that were previously destined for the landfill.
For more information, or to enquire about purchasing, please contact us here.
5. Phase 2 - Expansion of the PPRF and Request for Proposals
Phase 2 includes the expansion of the PPRF to add a processing capability of an additional 10,000 tons per year, bringing the PPRF to 20,000 tpa.
Developments within the industry have led to the emergence of new technologies and technology providers. As part of Phase 2, we will be going out to Requests for Proposals to identify, evaluate feasibility, and implement a complementary technologies such as cement aggregate, pyrolysis, or other technology for the balance of the tonnage generated by our PPRF.
For more information or to be kept up-to-date with the Request for Proposals, please contact us here.
Education
As with every recycling and recovery program, education has to remain an integral part of the process. Firstar Fiber’s IPWMS will provide several opportunities for sharing best practice and education:
Education for Waste Generators: Best use and recovery options for wasted resources. Demonstrating that all plastics are worthy of recovery.
Sharing Best Practice and Lessons Learned: Integrated systems allow for developing better methodology for the handling of plastic wastes and base data for end-market development
Demonstration of the Model: Lessons learned that can be replicated with bolt-on operations at other MRFs across America and the World